What we do
In addition to CNC machining, we also deal
with additional machining such as:
Tumbling
Polishing
Thread
Grinding
Mounting
Heat treatment
Surface treatment
Warehouse
Packaging
Customer portals and inventory management
Turnery
Kanban – consignment stock
PRODUCTION/SERVICES
Drilling
Thanks to advanced machine tools and technologies such as CNC drills, drilling has become increasingly accurate and faster, improving the quality of final products and reducing production time.
Milling
Milling allows material to be removed from a blank to create flat surfaces, grooves, and three-dimensional profiles, ensuring high precision and quality finishes.
Polishing
Brightening is a surface treatment used to make materials such as metals, plastics or glass shiny and lustrous. It is done by chemical, electrochemical or mechanical processes that smooth the surface, removing micro-imperfections and giving a mirrored or reflective appearance.
Tumbling
Tumbling is a mechanical process that uses a machine (the tumbler) to finish surfaces of materials such as metals or plastics. Through rotary or vibratory action, combined with abrasives and sometimes liquids, it removes imperfections, burrs, and sharp edges, improving the appearance or functionality of parts.
Washing parts with solvent
Grinding
This process uses abrasive tools, such as grinding wheels, to remove material in a controlled and precise manner, ensuring very tight dimensional tolerances.
WHERE
START FROM?
The steps leading from the receipt of a request
for a quote to the delivery of the particular product
are as follows:
0.
CUSTOMER REQUEST
1.
Verification of the design
by testing
2.
to be performed
3.
for raw material
4.
Quote
5.
Quote
6.
of parts
7.
8.
and delivery of finished parts
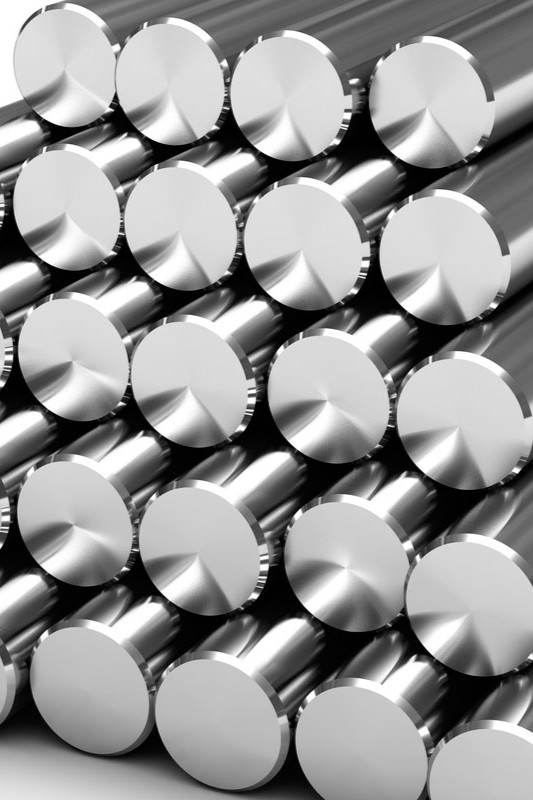
CHECK
RAW MATERIAL
TREAT:
- All types of steel
(including 11SMnPb, 35SMnPb, 39NiCrMo, 18NiCrMo, 17NiCrMo, AISI 303, AISI 304, AISI 630)
ferrous and nonferrous, in particular:- automatic steels
- case hardening steels
- quenched and tempered steels (alloyed and unalloyed)
- special steels
- stainless steels
- aluminum in the various alloys
- All types of Brass
- Titanium
- Various types of plastic materials
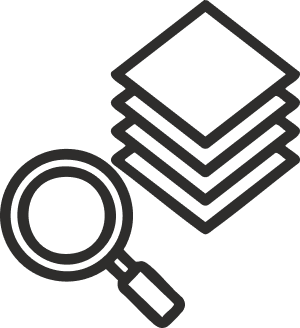
TREATMENTS
We rely on various certified external suppliers for heat and surface treatment processing of the particular products such as:
- Reclamation
- Cementation
- Aging
- Carbonitriding
- Temper
- Nitriding
- Annealing
- Passivation
- Phosphating
- Burnishing
- Anodizing
- Chrome plating
- Nickel plating
- Engravings
- Sandblasting